能源是现代社会存在与发展的基石,随着中国“碳中和”目标的提出,大规模开发和利用清洁能源已成为我国能源战略中的重要组成部分。在各类新型清洁能源中,光伏发电受到广泛关注。目前,我国光伏产业正以每年30%的速度增长,而光伏发电设备的主要原料晶硅电池片工厂亦急需提升智能化、自动化能力,以匹配快速增长的市场需求。
某新能源集团电池片生产工厂以“中国制造2025”为指引,打造高端光伏晶硅电池片智能制造工厂。
国自光伏晶硅电池片工厂AGV智能搬运整体解决方案,能实现大规模智能物流机器人物料转运,替代原有人工作业模式,大幅提升产能并持续保证生产线稳定运行。
痛点显现 制约行业发展
光伏产业的快速增长,带动市场对晶硅电池的生产强劲需求,国内各大新能源生产企业已在大范围布局太阳能晶硅电池片生产工厂。但当前晶硅电池片工厂仍以劳动密集型作业模式为主,对企业而言普遍存在如下痛点:
生产现场要求24小时连续作业,作业人员3班轮替,劳动强度大,导致人员流动性较大,企业管理成本剧增。
人工在生产设备前上料时,双手只能同时操作单个电池片载具依次上料,效率低下。
生产工艺复杂,对物料上料时的摆放、朝向、整齐度都有严格要求,要求作业人员低容错率和规范化作业。
不同工艺环节之间由人工完成物料的搬运与上料,中间环节物料信息缺失,异常原因难以追溯。
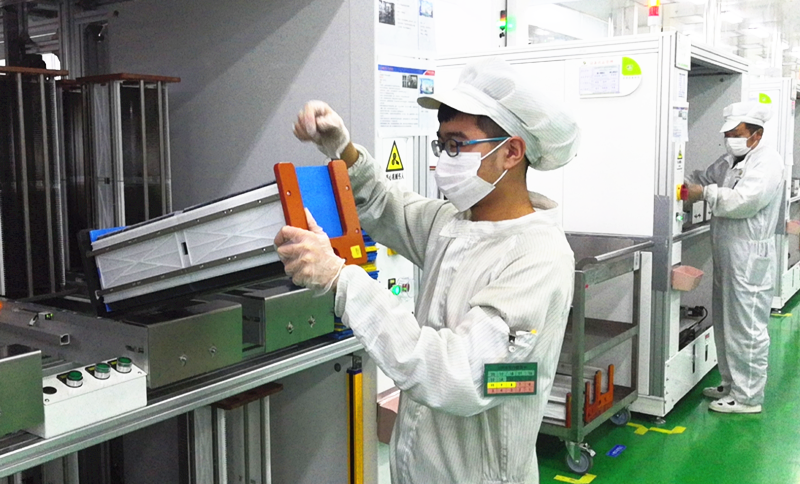
创新应用 助力产业升级
项目针对目前光伏晶硅电池片工厂存在的问题,在光伏行业某新能源工厂中通过AGV智能搬运系统,自动完成电池片的自动上料、下料搬运与线边暂存,以及生产过程中的信息记录与管理,全面解决客户痛点。
方案亮点
避免污染,实现零差错率
电池片工厂对洁净度要求较高,采用机器人搬运避免了人工操作对于电池片的污染隐患,且全程系统自动化协同控制,将货物配送差错率降低至零。
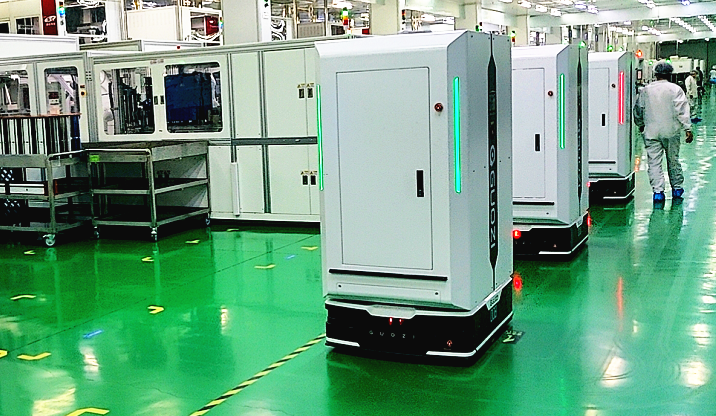
精准对接,确保易碎货品搬运安全
针对光伏行业物料平稳运输要求,单次搬运容量最高可达10个电池片花篮,满足电池片生产工艺产能要求。机器人通过视觉二次定位和上装自适应功能,实现辊道与对接机台±2mm的高精度对接,确保易碎物品搬运安全。
实现生产过程智能管理,提高良品率
生产过程全程实现无纸化与自动化,所有机器人作业过程,均由调度系统后台自动协同分配,实现任务可视化管理。整个工厂的产能变化,机器人运行路径、运行状态、任务状态信息均一目了然,有效避免了电池片上料错误和信息丢失,实现智能管控。
监控界面
实现24小时生产,搬运对接效率提升60%
该项目共投入使用数十台辊道机器人,实现24小时不间断作业,代替原有30个人力投入(10人/班次)。单个辊道机器人单次搬运10个电池片花篮,并支持10个花篮同时上料或下料,较传统人工依次上料的方式,效率提升明显。
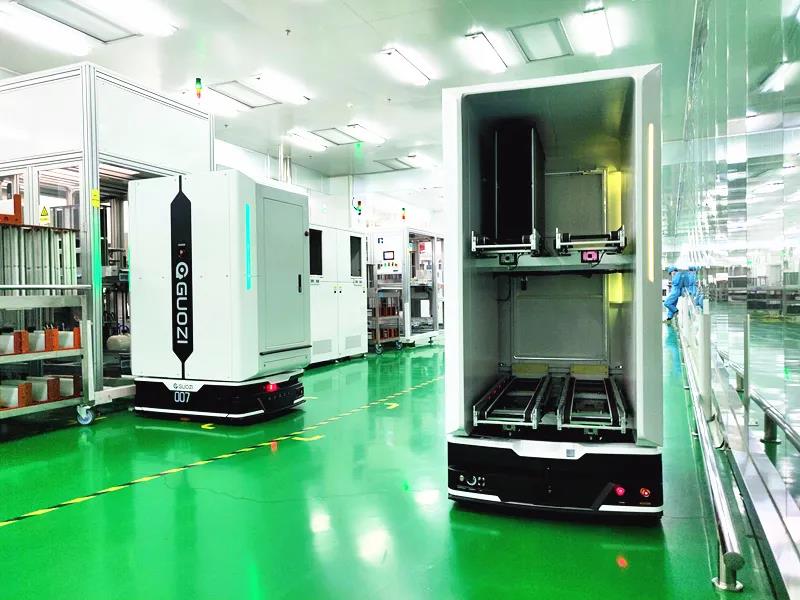
效益显著 具备推广价值
国自光伏行业晶硅电池生产线智能搬运解决方案,充分结合光伏行业特点,成功解决了传统型电池片工厂高人力成本和低搬运效率的问题,助力客户打造系统化、自动化、智能化的生产流程。
国自在该项目中应用的Slam导航配合侧向视觉二次定位功能和上装自适应功能,不仅适用于光伏电池片生产场景,亦可广泛应用于3C、面板和半导体等高精尖行业中,实现机器人与自动化产线的高精度、自动化无缝对接。
目前,该项目已建成面向全球开放的“光伏制造+互联网”透明工厂,国自助力客户企业成为光伏领域“中国智造”领军企业。